1, the impact of manganese on austenitic stainless steel
In the chromium-nickel austenitic stainless steel, manganese content is generally not more than 2%, and normal production is controlled at about 1.5%. And in the recent development of high nitrogen austenitic stainless steel, in order to improve the solubility of nitrogen, there is now a high manganese content (5%-10%) of chromium-nickel austenitic stainless steel. In the section nickel austenitic stainless steel, manganese is a very important alloying element, its main role is to be added to the steel with nitrogen, nickel and other elements that strongly form austenite compound to save nickel in austenitic stainless steel.
(1) The effect of manganese on the organization
Manganese is a relatively weak austenite forming element, but has a strong role in stabilizing austenite. When the chromium content of the steel is greater than 14%-15%, in order to save nickel, only by adding manganese is unable to obtain a single austenitic organization. As the chromium content in stainless steel must be greater than 17% to have more satisfactory corrosion resistance, so the current industry has been applied and incorporated into the standard manganese substitute for nickel austenitic stainless steel is mainly Cr-Mn-Ni-N type steel, such as 1Cr17Mn6Ni5N and 1Cr18Mn8Ni5N, etc..
Research shows that: steel manganese content is less than 2%, the change of manganese content on the commonly used Cr-Ni austenitic stainless steel organization (including the stability of austenite) has no significant impact.
(2) the effect of manganese on performance
In Cr-N austenitic stainless steel, with the increase in manganese content strength increase in nickel-free Cr-Mn-N austenitic stainless steel at low temperatures will appear ductile-brittle transition. These are very different from Cr-N austenitic stainless steels. When nickel is present in Cr-Mn-N steel, its low-temperature toughness can be significantly improved. This shows that only manganese and nitrogen without nickel austenitic stainless steel (Cr-Mn-N steel) can not obtain the excellent low-temperature toughness of Cr-N austenitic stainless steel.
Manganese in chromium-nickel austenitic stainless steel in addition to the role of deoxidation, one is hoped that it can stabilize the austenite; two is to improve the thermoplasticity of steel, three is with the strong affinity of manganese and sulfur to form manganese sulfide, both conducive to the removal of sulfur in steel, but also to eliminate the harmful effects of residual sulfur in steel. But further research shows that the presence of manganese in steel, precisely because of the formation of manganese sulfide, often leading to chromium-nickel austenitic stainless steel resistance to chloride pitting corrosion and crevice corrosion is reduced. Domestic in a series of research work based on some special steel mills have been 18Cr-8Ni type austenitic stainless steel in the manganese content down to 1.0% or less, the actual control in about 0.5%. This not only saves the manganese in the steel, but also reduces the manganese sulfide content in the steel and improves the pitting resistance of the steel.
Research shows that to chromium-nickel austenitic stainless steel to add more than 2% of manganese, except for some welding materials (welding wire, welding tape, etc.) is to improve the weld resistance to warm tendency (generally add 3%-7% manganese), there is no beneficial effect on its corrosion resistance, and in some conditions is even harmful.
As for manganese instead of nickel, nickel and nickel-free austenitic stainless steel, its corrosion resistance depends mainly on the content of chromium, nickel, molybdenum and nitrogen elements in the steel, and manganese role is very little, which is determined by the corrosion resistance of manganese itself. There is a high Cr-Ni-Mo austenitic stainless steel to add 3%-10% manganese to improve the solubility of nitrogen in steel (up to 0.5% nitrogen at atmospheric pressure), so that such steel in high Cr (20%-25%), high Mo (5%-8%) conditions still have a single The austenite organization and inhibit the precipitation of harmful chromium nitride, and corrosion resistance can reach or even exceed the level of some high nickel corrosion-resistant alloys. The emergence of such steels to fill the long-standing stainless steel and high nickel corrosion resistant alloy between the lack of high corrosion resistance, high grade of high chromium molybdenum stainless steel gaps. Representative grades are 00Cr24Ni22Mo7Mn3CuN0.5 (654SMo)
2, manganese on austenitic + ferritic duplex stainless steel
In Cr-Ni austenitic stainless steel, the amount of manganese in the steel is reduced (<2% later), the corrosion resistance of the steel is improved. Study the effect of manganese > 2% on the organization and properties of 0Cr25Ni5Mo3 duplex stainless steel, but when the amount of manganese in steel up to about 8%, also did not observe any changes in the amount of γ phase in steel. mn also has no significant effect on the strength of steel, plasticity, only when Mn ≥ 5%, the hardness of steel increased, which is related to the presence of σ phase and other precipitated phases in steel; in 750-950 ℃ aging Mn has a strong role in promoting the formation of σ-phase and significantly reduces the toughness of the steel; with the increase in the amount of manganese in the steel, its pitting resistance decreases, and the decline in these properties is related to the formation of MnS or σ-phase precipitation and depletion of chromium.
In order to make Cr-Mn-N (-Ni) system stainless steel to obtain pure austenite organization, generally need a higher content of Mn, Ni, N and other elements. And to obtain α + γ duplex organization structure, the required Mn, Ni, N content of the elements is relatively small, the cost of steel is also relatively low, at the same time, can also have some of the characteristics of α + γ duplex stainless steel. This is also an important role of Mn in duplex stainless steel.
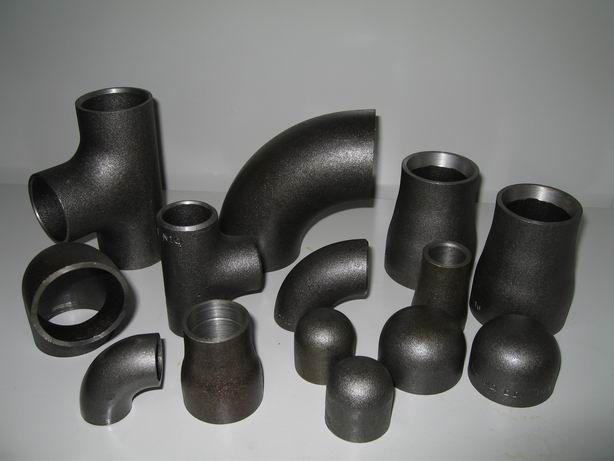
3, the development prospects of chromium-manganese stainless steel
Chromium manganese stainless steel is a more suitable for the current stage of China’s national conditions of cheap economic stainless steel, it is nickel saving, economic, cost-effective, good quality. Such as grade 1Cr17Mn6Ni5N containing Mn5.50 % to 7.50 %, Ni3.50 % to 5.50 % , 1Cr18Mn8Ni5N containing Mn7.50 % to 10.00 %, Ni4.00 % to 6.00 %. Chromium manganese stainless steel is mainly used in the field of consumer goods, than the current large use of chromium nickel stainless steel nickel savings of 3 % to 5 %, in the current nickel price, saving costs of about 30 %, so its price is lower, more popular, quality and function can also meet the general requirements of use, almost all the general food utensils, cabinet equipment and utensils, building decoration and other products, consumer goods field can be used. In the weak medium corrosion conditions can partially replace the chromium-nickel stainless steel, such as 201, 202, respectively, instead of 301, 302, 204Cu and 211 instead of 304; in the non-corrosive or weak corrosion conditions, in the decoration, urban construction and other key use of its aesthetic function of the application area is also very wide. And with the development of China’s economy, people’s living standards and the development of a huge rural market, its application areas and consumption will further increase.
Cr-Ni-Mn-N austenitic stainless steel is the type of stainless steel that began extensive research in the 1930s and 1940s. Its initial purpose is mainly to austenite forming elements N, Mn into the steel to replace the precious metal Ni, so as to save resources and solve the problem of Ni resource scarcity. With the development of metallurgical technology, to the 1960s and 1970s, the emergence of pressurized metallurgy technology, so that the solubility of N in steel under normal pressure is very small can be added to the steel more, and now can be added to 2.3%. the main role of N added to a significant improvement in the mechanical properties of steel, and the second is to significantly increase the ability of steel to resist local corrosion.
Compared with Cr-Ni austenitic stainless steel, Cr-Ni-Mn-N austenitic stainless steel is the biggest difference is the addition of a large number of Taikin elements Mn, N, which brings a series of performance changes. n in stainless steel, the reason for the great concern, mainly with its role in stainless steel closely related. Research shows that N is very strong formation and stabilization of public opinion and expand the austenite phase zone of the element. It is estimated that 1kgN is equivalent to 6 to 22kg Ni. There are many reports on this, and many formulas for calculating the nickel equivalent have been proposed. In the formula for calculating nickel equivalent, Simmons et al. proposed more precise.
Nieq = Ni + 0.12Mn – 0.0086Mn2 + 30C + 18N + 0.44Cu
As can be seen, the effect of N on the stainless steel matrix organization is quite strong. this role of N makes it possible to replace some of the Ni in stainless steel, reducing the ferrite content of steel. Can make austenite more stable, to prevent the precipitation of harmful intermetallic phases, and even in cold working conditions can avoid the martensitic transformation.
The effect of N on the mechanical properties of stainless steel, highlighted by: N in significantly improve the strength of stainless steel at the same time, and does not reduce the plastic toughness of the material, which provides a way to study the high strength and high toughness steel. Industrial steel shows that the addition of N, so that the strength of stainless steel than the steel without N increased by 2 to 3 times. In addition, N also improve the creep, fatigue, wear resistance of stainless steel. n improve yield strength in four main ways: solid solution strengthening; grain size effect; deformation hardening; precipitation hardening. n on the corrosion resistance of stainless steel beneficial effect is expressed in the resistance to intergranular corrosion, pitting corrosion, crevice corrosion. n on intergranular corrosion is more complex, it is generally believed that the n content of 0.16% or less, the resistance to intergranular corrosion The mechanism of N on intergranular corrosion is mainly: N delays the nucleation and growth process of Cr-rich carbides; reduces the activity of Cr in steel; the formation of chromium chloride precipitation, reducing the precipitation of Cr. In contrast, the beneficial effect of N on pitting and crevice corrosion is more obvious. the Wirksumme pitting equivalence formula expresses well the good effect of N in this regard.
PRE=%Cr+3.3%Mo+16%N
Grabke reported the effect of nitrogen on the critical pitting temperature (CPT) and critical crevice corrosion temperature (CCT) as follows.
CPT(°C)=2.5%Cr+76%Mo+31.9%N-41
CCT (℃) = 3.2% Cr + 76% Mo ten 10.5% N-81
In order to improve the solubility of N, the element Mn is added in large quantities. In the section nickel austenitic stainless steel, Mn is a very important alloying element, its main role is to be added to the steel with a strong austenite forming element N compound to save Ni in austenitic stainless steel. mn is a relatively weak austenite forming element, but has a strong austenite stabilizing effect. cr-Ni austenitic stainless steel, with the increase in Mn content increases strength. In the Cr-Mn-N austenitic stainless steel without Ni at low temperatures will appear tough brittle transformation phenomenon.
Mn, N instead of Ni section Ni and Ni-free austenitic stainless steel, its corrosion resistance depends mainly on the content of Cr, Ni, Mo, N and other elements of steel, while the role of Mn is very little. At present, the development of mature steel grades are mainly 200 series and Armco’s Nitronic series. There are also a number of steel grades that are under extensive research.